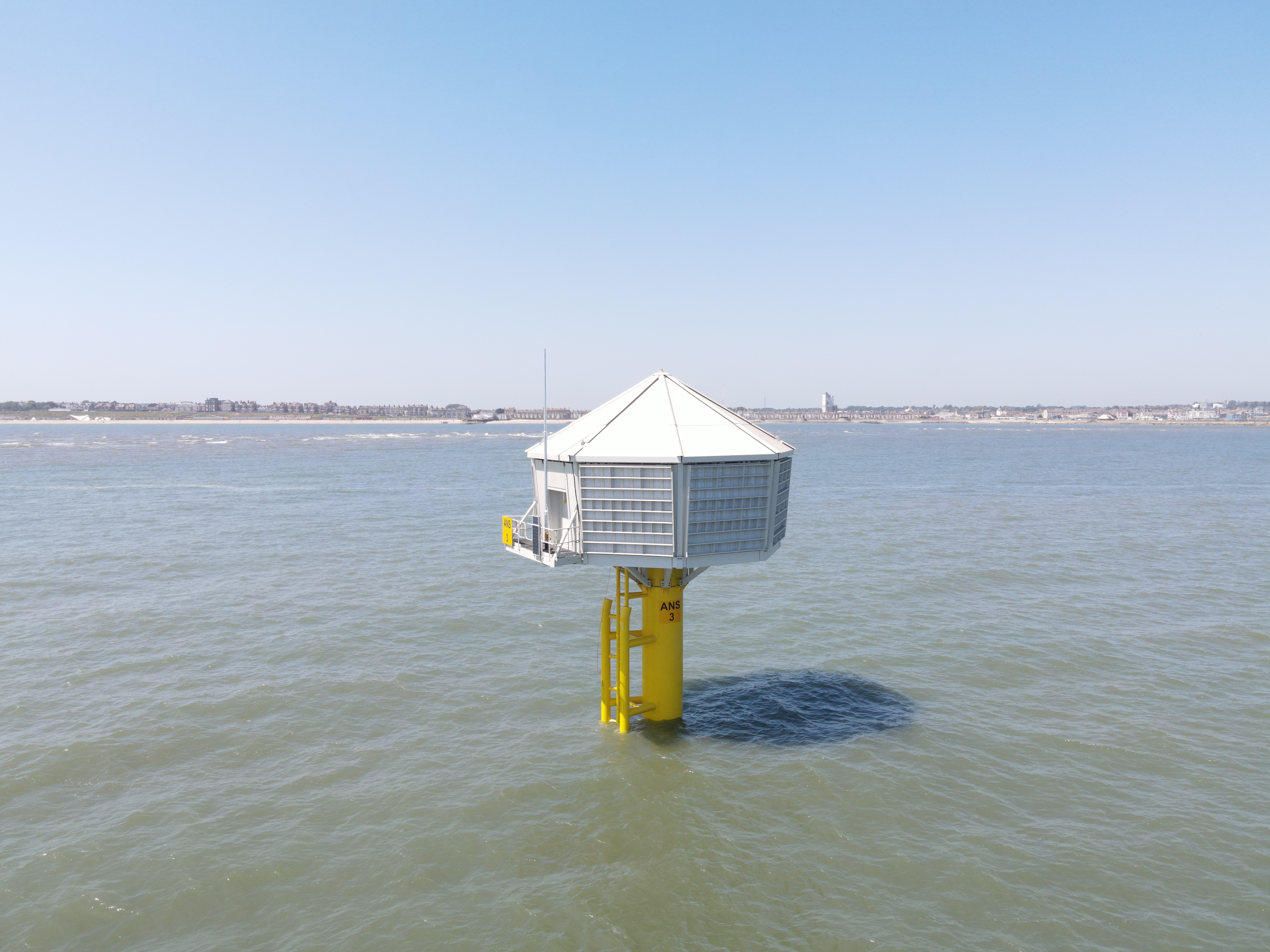
Red7Marine has recently completed the installation of three nearshore artificial nesting structures off the East coast at Lowestoft and Minsmere on behalf of its Client, Orsted.
Red7Marine’s involvement with the project spans back to August 2022 when we began working with Orsted and its principal designer Royal Haskoning along with Red7Marine’s fabrication partners in the completion of the design of the three artificial nesting structures.
There were four critical interfaces for this project and each element was fabricated at four separate locations with four different approved suppliers in Red7Marine’s supply chain, in addition to Red7Marine’s own in-house fabrication department.
Readmans steel in Middlesbrough supplied the steel tubes and fabricated the 3 no. 1620mm dia x 20mm thk monopiles. Each pile was in excess of 33m length. These piles comprised of butt-welded sections and in internal grout cap, and were painted traffic yellow. During installation these formed the foundation for the pile sleeves and nesting structure. The piles were driven approximately 10m below seabed.
Cleveland steel and tubes (CST) provided the batch material for the upper sections of pile sleeve which was connected to the base of the nesting structures, and also to the upper face of the main pile sleeves. The same batch material was also used for the main piling sleeves that sat over the monopiles. This steel tube was 1829mm dia x 22mm thk.
Armultra in Great Yarmouth fabricated 3 no. pile sleeves to site over the top of the monopiles and support the artificial nesting structures. The sleeves incorporated boat landing fenders and access ladders. Also within these sleeves were critically interfaced flange faces that had to marry up to the flange faces on the pile sleeve section, as well as a grout sleeve arrangement at their base internally to retain grout during pouring.
Four Tees Engineers in Fareham created the fabrication drawings from Royal Haskoning’s design for the artificial nesting structures, the pile sleeves and also the piles. They also fabricated the artificial nesting structures which comprised of upper pile sleeve connection, floor beams and durbar flooring, nesting panels from steel and polycarbonate, roof beams, roof panels, internal cages, ladder access systems and external balcony arrangements. All components were fabricated in kit form, and shipped to Lowestoft, where they were assembled by Four Tees Engineers steel erection teams.
Red7Marine in Ipswich fabricated the temporary works at its Port fabrication facility, which included a bespoke piling gate, a critically engineered pile sleeve lifting frame and the artificial nesting structure support stands upon which the main structures were assembled. Other temporary works fabricated by Red7Marine were CTV access ladder frames, ballast support frames and navigation masts for the jack up barge. Red7Marine engineers designed the support stands, ballast support frames, nav masts and CTV ladder mounting frames.
MintMech Engineers in Penryn, Cornwall designed the bespoke piling gate and pile sleeve lifting frame that Red7Marine fabricated and the pile sleeve grout sleeve modification that Armultra fabricated. They also designed and fabricated the pile upending frame and piling hammer stand.
The critical interfaces on this project were the pile sleeves which Armultra fabricated, the upper pile sleeve connection that was part of Four Tees Engineers’ scope, and finally the pile sleeve lifting frame which Red7Marine fabricated. It was crucial that one engineering surveyor was used to align and set out all three of these interfaces, and the Services of McPhilemy Surveying Services was utilised in this aspect to great effect ensuring accuracy and alignment of all elements.
Effective supply chain management was essential to this project for all preconstruction fabrication works even before Red7Marine had a footprint on the project mobilisation site in Lowestoft. This was managed and overseen by Red7Marine’s Head of QHSE and Business Improvement – Mark Smith who worked closely with Richard Readman (Readmans Steel), Luke Harman and Karl Pull (Armultra), Craig Wilkinson, Dave Lemon and Alistair Drain (Four Tees Engineers) and Laurie Thornton, Leigh Frazer and Dan Benson (MintMech Engineers) and Jamie Bowes, Jason Hatcher, Trevor Vincent, Jacob Hampton (Red7Marine).
Red7Marine with its project partners proved to be a formidable team on this high-profile project.